What is Blasting?
What is Blasting?
Blasting is a surface processing method in which countless abrasive particles are sprayed, thus colliding with the workpiece to roughen, grind, or polish the surface.
Blasting is generally a dry process. However, depending on the method, it is classified into several types such as Sand Blasting, Blower Blasting, and Shot Blasting. It is also used for various purposes such as rust removal, cleaning, and polishing. Especially well-known applications include glass craft patterning and lettering of tombstones.
This page provides an overview of the blasting process in general, its features, types, applications, general merits and demerits, and Wet Blasting.
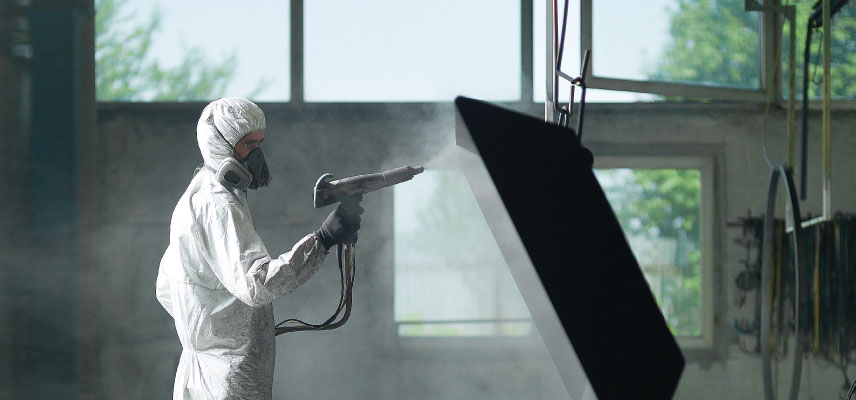
Incidentally, blasting is a kind of "free abrasive processing".
There are two types of processing using abrasives. One is "fixed abrasive processing" that uses tools with fixed abrasives such as belt grinding, tape grinding, and sandpaper, as well as polishing and lapping. The second is "free abrasive processing" in which the abrasive is mixed with a liquid and the surface is polished or ground in a state where it moves freely, and the blasting process corresponds to the latter.
The Origin of Blasting
It is said that the origin of the blasting method was around 1870 when a U.S. engineer named B.C. Tillman invented a device for spraying emery sand and named it "sandblasting".
Tillman is said to have come up with this invention after noting that the window glass fogged up after a sandstorm in a seaside town.
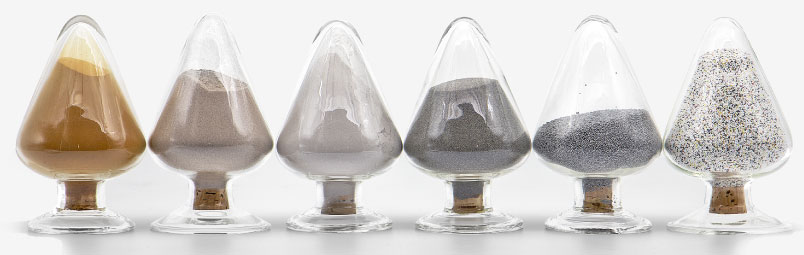
Blasting Characteristics
Blasting, in which abrasive particles directly hit against an object to process it, has various characteristics as shown below.
Physical Processing
All methods of blasting are physical processes that produce effects by physically hitting, scraping, or rubbing an object, and do not use chemicals or organic solvents.
Constant Processing Force
In blasting, which is free abrasive processing, no further external force is applied to the particles once they are sprayed or blasted.
Therefore, the processing force is determined by the mass, speed, and shape of the particles at the time of blasting, and processing is performed with a constant force within that range.
The processing surface has no directionality.
When a large number of particles are projected with a constant force and collide with the object, a large amount of unevenness corresponding to the size of the particles used is formed on the surface of the object.
This unevenness does not generate streaks like buffing or lapping, resulting in a non-directional, random uneven surface.
Effects change depending on type of particle selected
By changing the material, size, shape, impact speed, mass, etc. of the particles, blasting can achieve various processing effects.
For example, polygonal particles give you grinding effects and such, and with spherical particles you can get peening effects and such.
It can handle any type of material
Types of Blasting
Blasting can be broadly divided into two types: dry blasting and wet blasting, depending on the environment in which the particles are used.
Dry blasting includes sand blasting, blower blasting, and shot blasting, while wet blasting includes wet blasting and wet shot blasting.
Particle acceleration methods can also be classified into two types: mechanical and pneumatic.
Blasting Classifications
Sandblasting
Dry Type/Air Type
Sandblasting is a blasting method that uses compressed air from a compressor as energy for accelerating particles.
Generally speaking, more often blasting refers to sandblasting.
Water is not used and only particles are accelerated by compressed air for spraying.
They are separated by the difference in acceleration method: One is the "suction type," which uses the force of compressed air to suck and project the particles into the nozzle, and the other is the "direct pressure type," in which the particles in the pressurized tank are mixed and pressurized by air and projected.
Previously, it was called "sand" blasting because it used sand as an abrasive. However, today it uses ceramics such as alumina (aluminum oxide), as well as glass, plastic, metal and walnut powder as abrasives.
Sandblasting is often used for glass craft patterning and lettering of tombstones.
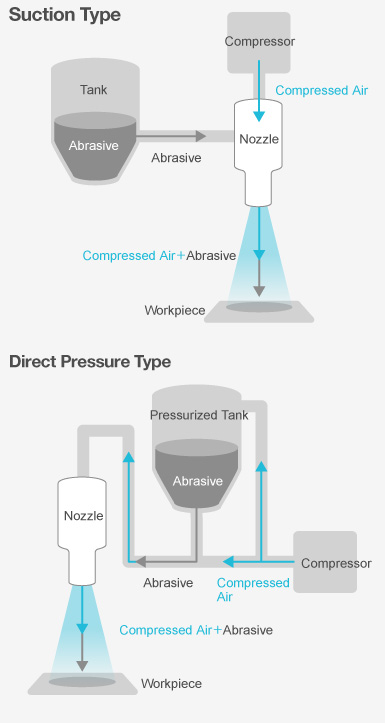
Blower Blasting
Dry Type/Air Type
This is a blasting method that uses a fan called a blower instead of compressed air to project or accelerate particles.
A blower has a lower pressure and weaker acceleration than that of compressed air from a compressor, and the processing is softer. However, it does not require a compressor that consumes a lot of energy, so it saves energy and keeps processing costs low. It is suitable for soft processing of large areas.。
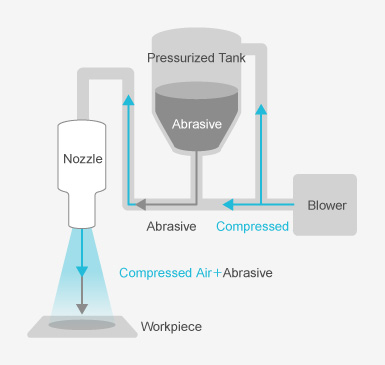
Suction Blasting
Dry Type/Air Type
In this blasting method, particles are sucked in while the processing area is completely sealed, and the abrasive material is placed in the air flow to scrape the surface of the object.
Since a blower (fan) is used for suction, there is no need for a compressor, and the cost is low.
Since no abrasive material is sprayed, no dust is generated and work can be performed in a clean environment.
By placing an abrasive at the inlet of the pipe and sucking it from the exit, the inner surface can also be processed.
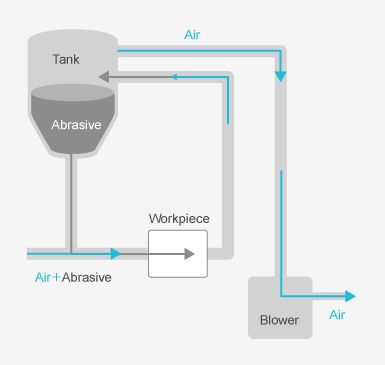
Dry Ice Blasting
Dry Type/Air Type
Among sandblasting, those that use dry ice pellets as an abrasive are called dry ice blasting.
Since the projected dry ice changes to a gas after colliding with the object, there is no concern about particle residue on the surface.
Also, there is no need to dispose of the used particles.
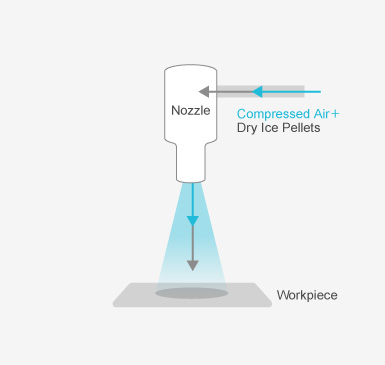
Shot Blasting
Dry Type/Mechanical Type
In this method, an impeller is rotated by a motor, and its centrifugal force is used to accelerate and spray the particles.
The particles used are often called blasting materials. And mainly metal abrasives such as steel, stainless steel, aluminum and copper are used.
In order to suppress scattering during spraying, particles must have a certain size and mass, and steel balls of about 1 mm are mainly used.
Abrasive material is projected over a wide area, so it is used for large-area and large-volume processing.
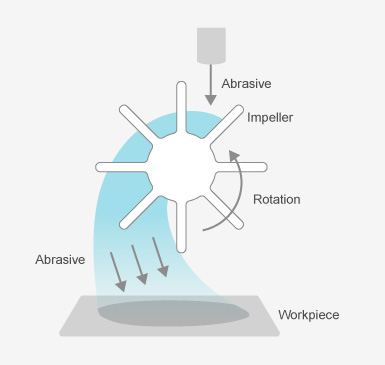
〇
- No compressor is needed, thus saving energy and cost.
- A large amount of particles can be projected over a wide range, and uniform processing of large areas is excellent.
Wet Blasting
Wet Type/Air Type
It is also known as "liquid honing". This is a wet blasting method in which a mixture (slurry) of water and an abrasive is accelerated by compressed air and sprayed.
Since the abrasive is always mixed with water, it does not scatter during spraying, even microparticles as small as a few microns in size, which cannot be handled by dry-type processing, can be used.
The scraped off dirt and sprayed particles are quickly washed away by the water. As a result, the surface can be processed and cleaned at the same time. Compared with the dry type, very little abrasive remains, which is a main feature of this method.
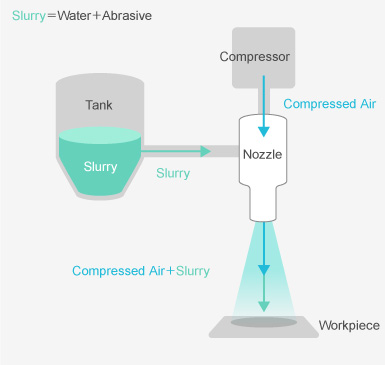
Wet Shot Blasting
Wet Type/Mechanical Type
This is a mechanical wet blasting method that sprays using an impeller and equipment is currently being developed by our company for practical use.
As with shot blasting, no compressed air is used, so no compressor is required. This is a next-generation blasting method that combines the characteristics of shot blasting, which can project particles over a wide area and can process large areas, and wet blasting, which allows for fine processing using very fine particles while doing cleaning and processing silmutaneously.
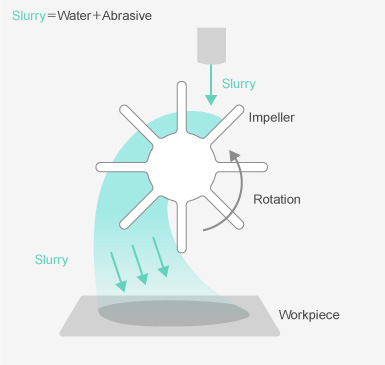
Blasting Applications
Although the application differs depending on each method, such as the strength of processing force and the difference in processing methods, this section will explain the applications in which the blasting method is generally used.
Rust Removal
The so-called "rust" that occurs on the surface when metal reacts with oxygen and moisture can be removed instantly without using chemicals.
Since blasting is a physical process, it is characterized by its ability to remove rust regardless of the material. So not just from steel, but also from aluminum, copper, and such.
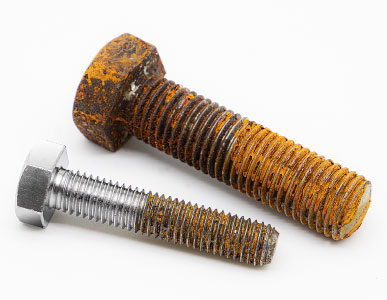
Die Cleaning
For the purpose of mass-producing industrial products, dies are used to create molds, and then materials such as metal, resin, and rubber are poured into them to form parts. So the dirt or grime such as mold release agents and molding material residue that adheres to the inside of this die can be removed.
Because fine particles can enter the gaps, even objects with complex shapes can be processed and the dirt removed.
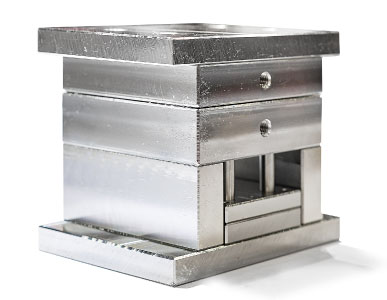
Satin Finish
It is possible to form countless fine irregularities called "textures" on the surface of metals, resins, and other materials. By changing the size, shape, or material of the particles used, it is possible to create a variety of textures.
The purpose of this textured processing is to achieve the anchor effect which improves adhesive strength, adds patterns, and improves wettability.
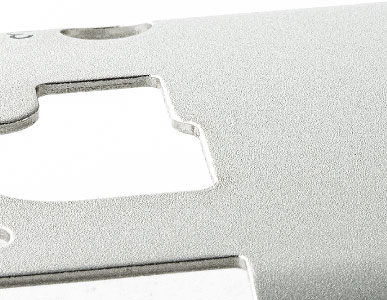
Deburring
Protrusions that occur when processing metals, resins, etc., and those that protrude from the joints of dies and harden during molding are called "burrs". Burrs cause various problems such as injury during product use and deterioration of quality. Therefore, they are removed by blasting if necessary.
Even burrs in small areas that are difficult to reach can be removed by blasting, thanks to its features of constant processing force and non-directionality.
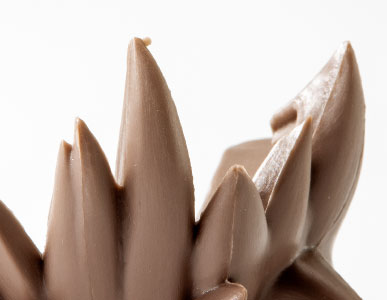
Polishing
Normal blasting scrapes the target surface to form a fine unevenness. However, there are also processing methods that can be do polishing (smoothening) instead of making holes.
In addition, by using a special abrasive suitable for this purpose, it is possible to eliminate unevenness on the surface and create a glossy mirror-like surface.
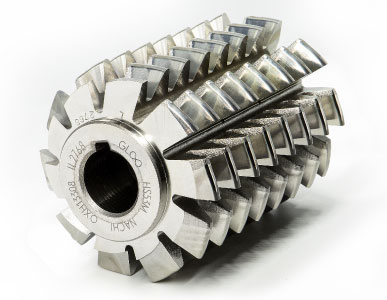
Benefits of Blasting
It can handle any type of material
Blasting is a physical processing method that processes by colliding particles on the surface, so unlike chemical processing, processing can be done regardless of the material of the target object.
Non-directional uneven surface
Since the processing force is constant, directional scratches such as thosed caused by brushes or buffers do not occur, and a uniform unevenness with no directionality can be achieved.
Wide range of processing effects
Demerits of Blasting
Only the areas that the particles hit can be processed.
Because the blasting can process only the section where the particles hit directly, it is necessary to apply the particles to the entire processed surface.
As a result, the processing time increases in proportion to the size of the process area, and it is difficult to treat narrow gaps and inner surfaces of cylinders.
Wearing down of the machine
When using particles with a strong grinding force, the machine itself is scraped and worn down because the processing chamber and the flow path of the particles are also processed simultaneously with the processing of the object.
Parts must be replaced regularly due to the higher processing power and faster wear in the pipes, the spray opening, etc., which are in the path of the particles.
Sludge is generated
Summary
In short, blasting is not suitable for each type, as it can be said that there are various types depending on the particle acceleration method, processing environment, and the particles used.
It's best to understand the characteristics of each blasting process and select the optimum processing method that suits the processing purpose.