Removal of the glass non-conductive layer from LTCC substrates
Processing Details
- Washing
- Removal
The glass non-conductive layer, which causes plating defects, is completely removed without any unevenness.
Wet blasting is a physical method that can remove LTCC glassy non-conductive layers without unevenness.
It creates an optimal surface for the subsequent formation of a good plating film without using any chemicals.
Contents
Do you have any problems like these?
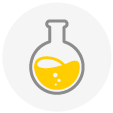
Chemicals are ineffective
The non-conductive layer that is generated during firing and must be removed is glassy and difficult to remove with chemicals.
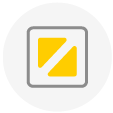
Left behind, electrodes collapse
Brush polishing and buff polishing tend to leave the non-conductive layer in the pattern and cause electrode crushing and scratches due to the pressure.
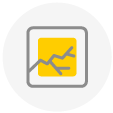
Excessive cutting
Brush polishing and buffing do not stabilize the amount of shaving, and overshaving causes a decrease in the bending strength.
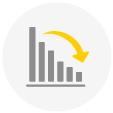
Tool management takes time
Brush polishing and buff polishing, in which the grinding force tends to change easily, requires time and effort to manage the tools and is inefficient.
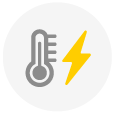
Frictional Heat & Static Electricity
Polishing by the current removal method generates frictional heat and static electricity that adversely affect product quality.
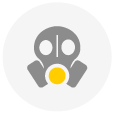
Dust
Dust generated from brushes and buffers creates a poor working environment, and there is a high risk of dust explosions.

Wet blasting solves the above problems and completely removes all of the non-conductive layer that causes poor conduction.
Macoho's wet blasting is a powerful ceramic cleaning method that uses fine particles of several microns in size, water, and compressed air to remove every inch of the glass non-conductive layer generated after firing in the manufacturing process without changing the surface shape of the LTCC substrate. This is a powerful ceramic cleaning method that creates a beautiful base shape that is ideal for plating.
LTCC surface cleaning with wet blasting
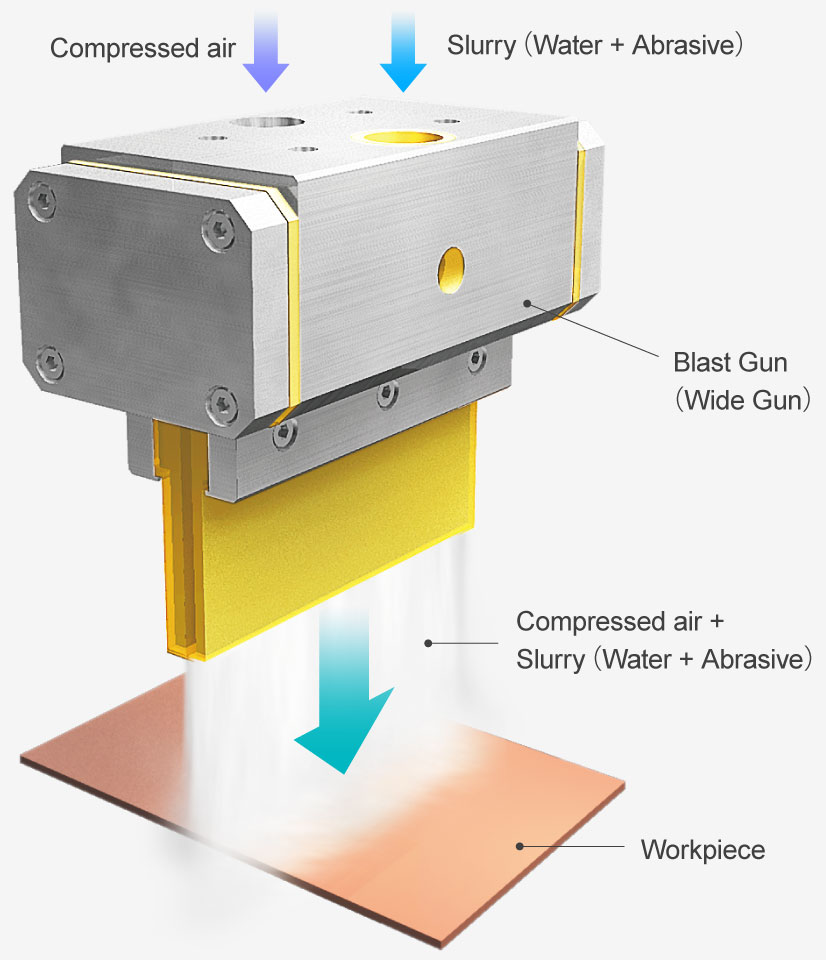
Wet blasting is a physical surface treatment method that uses fine abrasives.
The glass layer formed during firing, which is the cause of plating defects on LTCC (low-temperature co-fired ceramics) substrates, is removed evenly, creating an optimal surface for the subsequent formation of a good plating film.
Processing Examples
In the larger photo, you can see that even though the glass layer that impedes the electrical flow was removed, no unnecessary deformation occurred in the electrode. The small image to the side shows further magnified details. After processing, very dense irregularities are formed uniformly.
Surface condition before processing
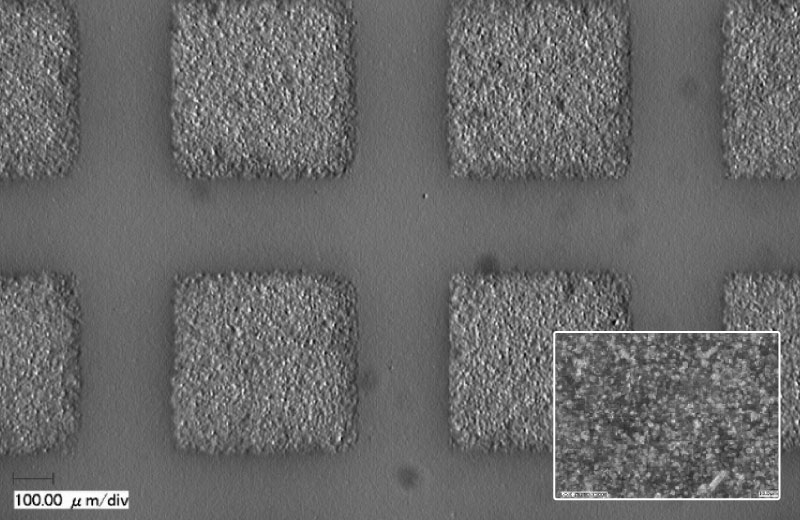
Surface condition after processing
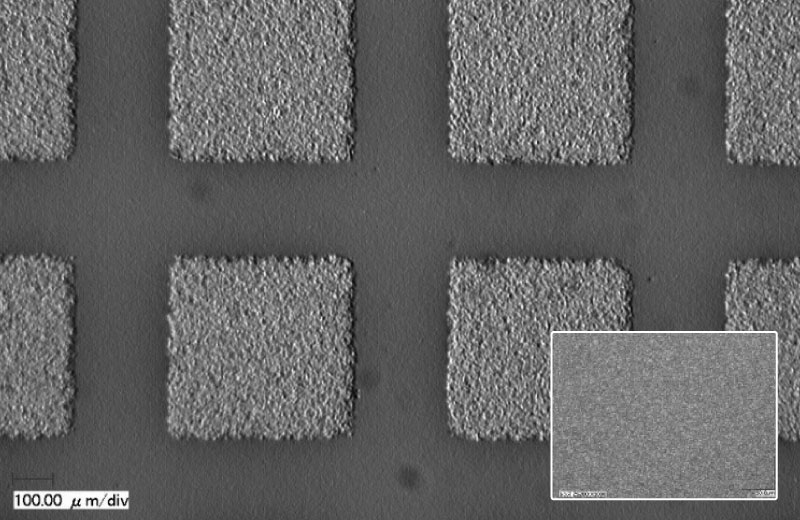
Features of LTCC surface-cleaning with wet blasting
Compared to other methods, LTCC cleaning with wet blasting has the following features.
Chemical-free physical method
Wet blasting is a physical processing method in which a mixture of abrasive and water is projected onto the object to remove the surface layer. Therefore, it is effective even for chemical-resistant glass materials, and it generates no reactive waste. In addition, since we use a system that circulates and reuses water and abrasive materials, we are able to design a sustainable process that takes into consideration the environmental impact.
No irregularities or damage
The fine abrasives of a few microns in size used in wet blasting can penetrate into the complex recesses on the substrate surface and evenly scrape off the non-conductive layer in every corner. In addition, the uniform mist projection causes almost no damage to the substrate surface. Wet blasting which has high controllability does not cause a decrease in bending strength due to excessive shaving.
Easy Automation
Wet blasting is a fluid process that uses water, making it easy to adjust processing volume and design systems. It is also easy to automate. In addition, since the removal of the non-conductive layer, rinsing, and drying processes can be continuously performed in a single machine, process control can be consolidated, and costs can be reduced through labor and manpower reductions in the glass layer removal process.
Simple daily management
Wet blasting equipment circulates the abrasive material and water used for processing, and the only item to be managed daily is the abrasive concentration in the water. In addition, an automatic sludge collection unit for crushed abrasives and wet blasting waste, and an automatic abrasive supply device to supply abrasives at a specified concentration can also be connected to the equipment. This enables both easy management and stable operation.
No Dust, No Heat, No Static Electricity
Wet blasting uses abrasive materials, but since the cleaning process is carried out in a wet environment, the abrasives do not scatter and almost no dust is generated. A good working environment can be maintained and there is no risk of dust explosions. In addition, since the abrasive material is constantly mixed with water and cooled and neutralized, there is no need to worry about frictional heat or static electricity, making it ideal for processing products where these should be avoided.
Optimum surface formation for plating
Wet blasting removes the glass layer while at the same time completes the surface treatment that is ideal for plating. When removing non-conductors, wet blasting forms dense, fine irregularities. These irregularities with a narrow pitch and height differences have a strong anchoring effect that increases adhesion strength, contributing to improved plating adhesion. In addition, the roughness can be finely adjusted by selecting the particles.
Comparison with brush polishing and buffing
The differences between wet blasting, brushing, and buffing.
Cleaning Power
In wet blasting, the abrasive of several microns in size penetrates into the uneven shapes and cleans them so there is no remaining non-conductive layer within the pattern. On the other hand, brush polishing and buffing are not good at processing uneven shapes, making it difficult to process every corner inside the pattern.
Controllability
Wet blasting makes it easy to control the processing force by choosing the particles that your needs and by using our unique wide gun for uniform processing. On the other hand, brush grinding and buffing are difficult to control because the amount of grinding varies with the degree of wear of the tool, making it difficult to stabilize the process.
Dust, Heat, Static Electricity
Wet blasting is a wet process, so it does not generate dust or static electricity, and it also has a cooling effect. On the other hand, brush polishing and buffing generate grinding debris that becomes dust. They also generate static electricity and heat from the friction.
Equipment Examples
We propose the following equipment according to the workpiece size and processing details. However, our equipment is essentially based on free design, in which the application and conditions are optimized for your company's processes. Our basic policy is to provide all our customers with optimal specifications. First, consult with us about the material and size of the workpiece, processing purpose, and equipment conditions. Our specialized staff will handle this.
Equipment for plate-shaped workpieces
- Automatic
Compact automatic equipment for simultaneous double-sided processing of lead frames and other thin plate-shaped workpieces.
Equipment for research and development
- Semi-automatic
Compact equipment suitable for research and development that automatically processes workpieces by using a wide gun on a single axis.