Steel bar descaling
Processing Details
- Removal
- Scraping
Clean, high-precision oxide scale removal that replaces shot blasting and pickling.
By using wet blasting for the "removal of oxide scale from steel bars" instead of "acid pickling", which generates large amounts of sludge and wastewater, and "shot blasting", which causes uneven processing, you can achieve precise, uniform processing and stable production of high-quality products.
Problems with Current Methods
Do you have any of the following issues in removing oxide scale by shot blasting, peeling, pickling, and such?
Shot Blasting
It cannot be used for finishing processes due to uneven processing and oxide scale residue. In addition, scale tends to be embedded in the bar surface due to the hammering of abrasive materials.
Peeling
It is a contact-type process, and the tool itself is subject to wear. There is also the possibility of core wobble, making it difficult to produce consistent quality or process at a uniform thickness. Furthermore, the amount of material that is removed tends to be relatively large.
Pickling (chemical process)
In some cases, uneven processing occurs at the contact areas between workpieces. In addition, the reaction generates large amounts of sludge and wastewater. Furthermore, since the process takes a relatively long time, it is necessary to maintain a large inventory.
Removal of oxide scale from steel bars by wet blasting
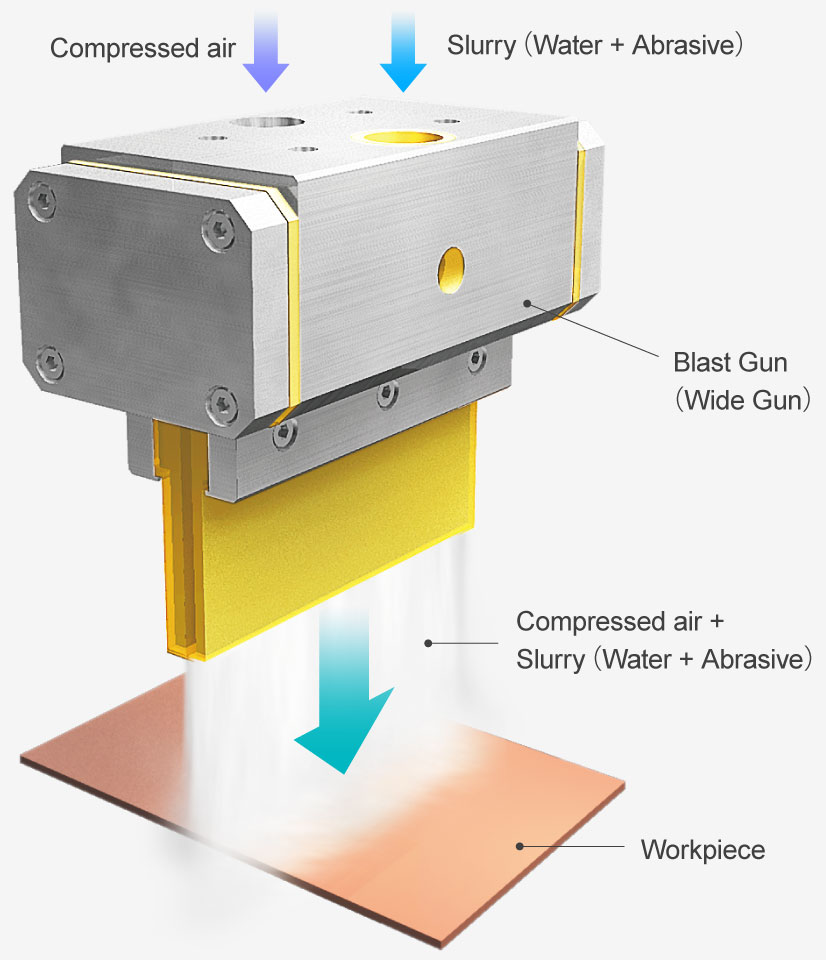
Our wet blasting equipment is characterized by precise, uniform processing and high controllability.
There is no uneven processing as with shot blasting, and because the surface is washed with water during processing, embedding of abrasives can be greatly reduced.
Furthermore, wet blasting is a non-contact process that does not wear out the tools. High controllability enables stable production of products of the same quality with the same processing power at all times.
Example of processing using wet blasting
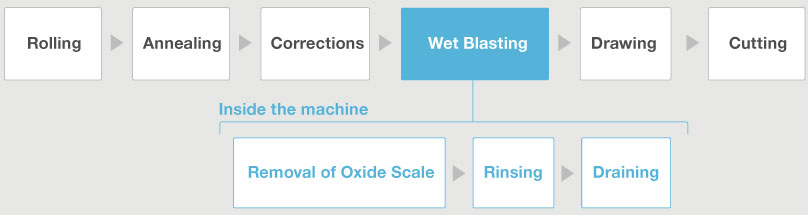
Advantages of Wet Blasting
The main advantages of replacing conventional processes such as shot blasting and pickling with wet blasting are as follows.
Full automation is easy
Our equipment can be compactly integrated into a single unit for scale removal, rinsing, and draining. As an example, we can integrate with the pre-processes of front-end rolling, drawing and cutting.
Improves the factory environment
There is no heat or dust as with shot blasting. In addition, there is no surrounding corrosion or unpleasant odors that occur with pickling. This allows work to be done in a clean environment and significantly reduces waste.
Compatible with a wide variety of materials
Wet blasting is a physical process. It can remove oxide scale from a variety of materials, including alloy steel, carbon steel, and stainless steel, without being affected by the chemical resistance of each material.
Equipment Examples
We propose the following equipment according to the workpiece size and processing details. However, our equipment is essentially based on free design, in which the application and conditions are optimized for your company's processes. Our basic policy is to provide all our customers with optimal specifications. First, consult with us about the material and size of the workpiece, processing purpose, and equipment conditions. Our specialized staff will handle this.
Wet blasting equipment for rod-shaped bar materials
- Automatic
Automatic equipment that wet blasts the entire circumference of rod-shaped bar material evenly and at high speed.