Surface treatment of glass
Processing Details
- Roughening
- Washing
- Scraping
Glass is finely roughened to Ra 10 nm
while maintaining transparency.
Only wet blasting can do "transparent roughening". Ultra-fine roughening of the topmost surface is possible without changing the optical properties.
Contents
What is glass surface treatment?
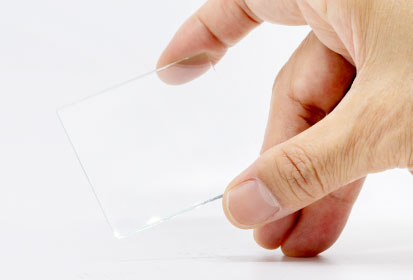
Glass surface treatment is a process that imparts various functions to the surface of glass.
Mainly, there are various types of processing depending on the purpose, such as "etching" to scrape off the surface, "AG processing (anti-glare treatment)" to form unevenness to prevent the reflection of light, "heat strengthening" and "chemical strengthening" to modify the surface, "coating" to form a protective film on the surface, and "roughening" as a pretreatment for coating and other processing.
Surface treatment of glass by wet blasting
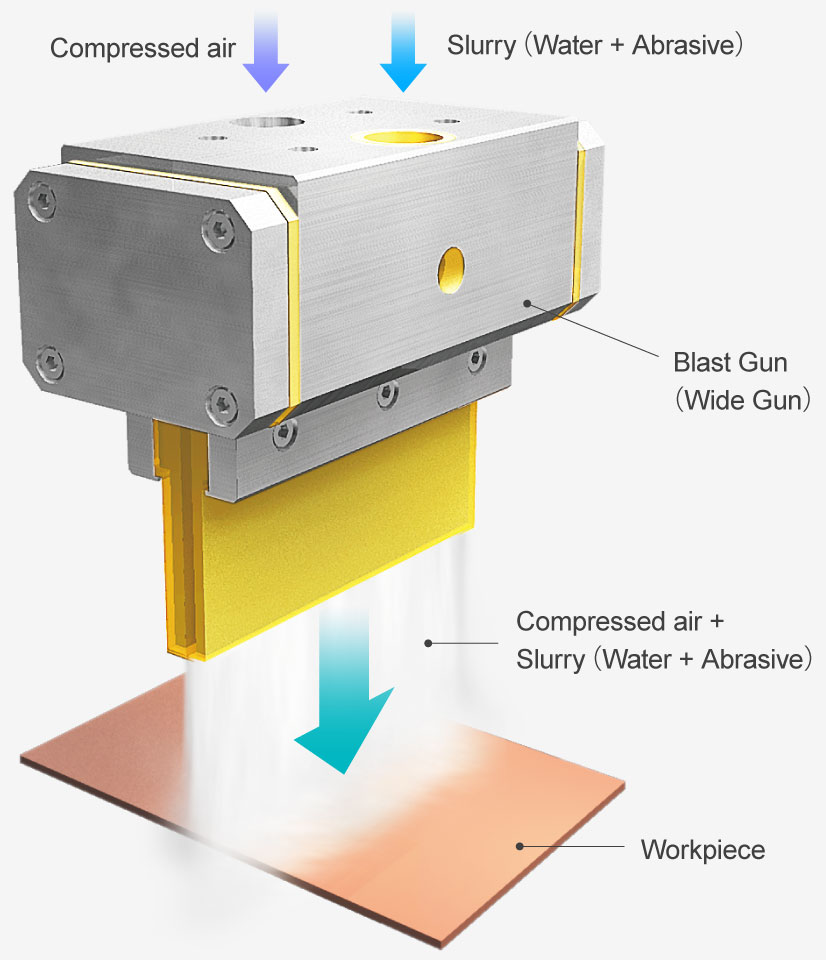
The surface treatment of glass by wet blasting is mainly "uniform micro-roughening of the glass surface."
Using a wide gun (our patented technology) that can uniformly process large areas and a fine abrasive material several microns in size, it is possible to form nano-level irregularities randomly and evenly on the glass surface.
The microscopic irregularities provide the glass surface with the effects of controlling reflectance and transmittance, improving wettability and adhesion, and reducing sliding resistance.
Main Applications & Actual Results
Micro-roughening of glass by wet blasting is mainly used in the following applications.
Pretreatment of AG Processing (Anti-Glare Processing)
Wet blasting creates a finer and more precise surface than dry blasting. Therefore, it is used as a pretreatment for high-definition AG processing.
Wet-Blasted Surface
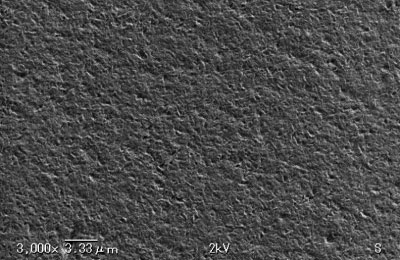
Surface conditions after the next process
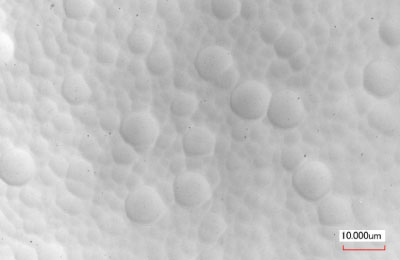
Pre-adhesion process for coatings and thin films
Wet blasting, which can use fine abrasives, forms "nano anchors" at Ra 10 nm, improving the wettability of glass and lens surfaces and the adhesion strength of coatings and thin films.
Titanium film formed on glass without pretreatment
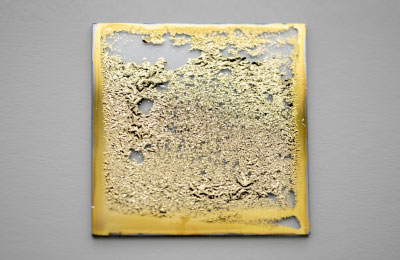
Wet Blasting Processed Parts
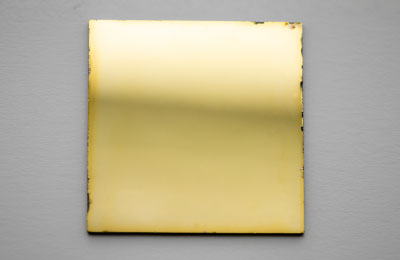
Flattening
Removes processed marks, altered layers, and brittle layers on the surface of glass and lenses to create a smooth surface. It also prevents the occurrence of pinholes (due to the presence of surface singularities) that occur in the post processes.
Quartz Glass Before Processing

After Wet Blasting

Surface Cleaning
Complete cleaning of difficult-to-see surface debris is done at high speed without damage. The strength is weaker than dry blasting but stronger than plasma. Furthermore, this cleaning process is also effective as a pretreatment for coatings.
Glass - Before Cleaning
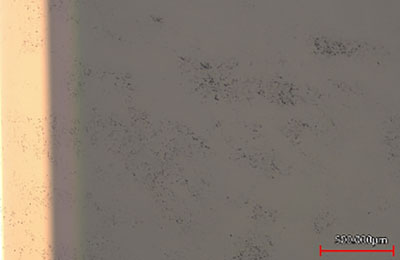
After cleaning with wet blasting
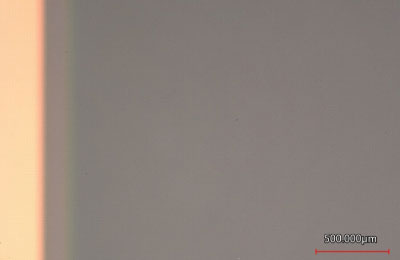
Features of glass surface treatment by wet blasting
Micro-roughening of glass by wet blasting has the following features when compared to other methods.
Fine irregularities
The roughness of the treated surface is determined by controlling the abrasive size and projection conditions. Wet blasting uses fine particles (~3 μm) to create finer irregularities compared to other blasting processes.
Damage Free
Compared to general shot blasting, this process can use abrasives that are 1/10 to 1/100 the size of those used in shot blasting, and thus can treat glass surfaces without causing cracks or other damage.
Transparent Roughening
Wet blasting can reduce reflectivity and improve wettability while maintaining the transparency of the target glass. This “transparent roughening” is a process that can only be achieved with wet blasting.
Improvement of wettability and retention
The fine irregularities (pins) formed on the surface by wet blasting suppress the contraction and expansion of the spread droplets and hold the liquid in place, improving the wettability of the target surface.
About fine irregularities and being damage free
With wet blasting which is a wet process, its main feature is that because it uses water as a medium, it is able to use very fine particles (~3 μm). Therefore, it can form finer irregularities than other dry blasting processes (dry blasting, sand blasting, air blasting, shot blasting). Also, this processing does not cause excessive damage to the target part.
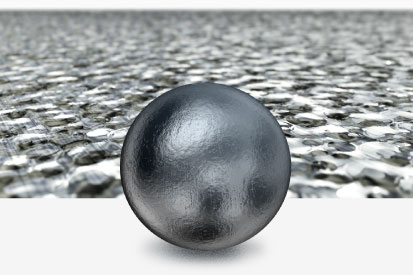
Spherical shot material (about 600 μm in diameter) and its processed surface image.
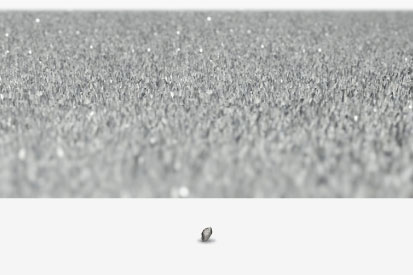
Wet blasting abrasive (about 6 μm in diameter) and its processed surface image.
About transparent roughening
Wet blasting, which uses fine abrasives, can form fine irregularities on the surface, reducing reflectance while maintaining transmittance, and can do roughening to improve wettability.
Changes in transmittance and reflectance after wet blasting
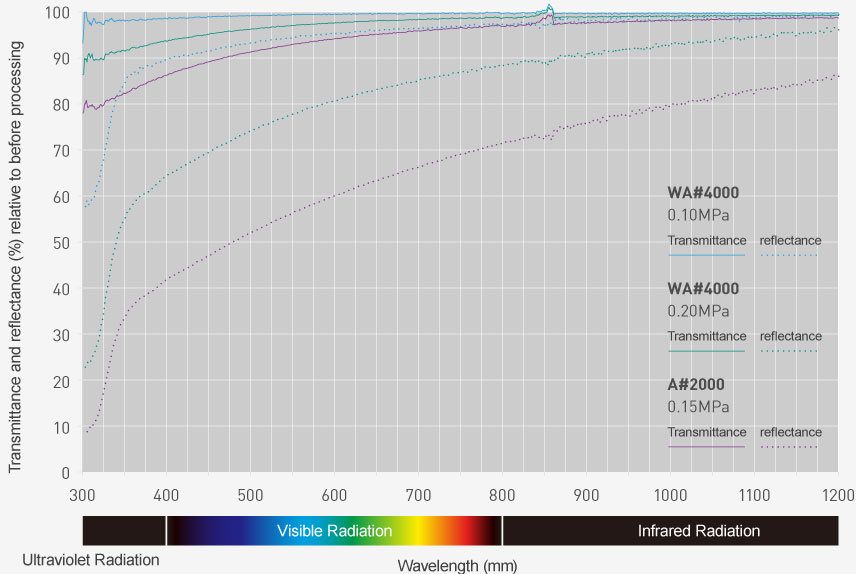
Workpiece Material: Blue Plate Glass
Processing Conditions: processing speed - 5 mm/sec, number of times processed - 2 passes
Improvement of Wettability and Retention
Fine irregularities caused by physical processing improve surface wettability and liquid retention. The fine irregularities (pins) formed on the surface by wet blasting suppress the contraction and expansion of the spread droplets and hold the liquid in place. This is called pinning.
Comparison with Other Methods
Comparison of glass surface treatment by wet blasting with various other methods.
Comparison with Dry blasting
In shot blasting, the abrasive is generally #800 (14 μm) or higher, which is larger than that used in wet blasting, and the processed surface is rougher than that of wet blasting, with the unevenness being more noticeable. However, the processing power is stronger than wet blasting. Dry blasting requires a separate rinsing process due to the large amount of embedded residue, while wet blasting requires relatively light rinsing because cleaning occurs simultaneously with processing. However, wet blasting requires a draining and drying process because water is used. Static electricity or heat may be generated depending on the conditions. However, these do not occur in wet blasting. Dust from abrasives is much less with wet blasting because the abrasives are mixed with water.
Comparison with Grinding
As a feature of grinding, scratches may occur due to the bite of foreign matter. In addition, a separate washing process is required. Compared to wet blasting, fine control of processing and consistent quality may be issues.
Comparison with Etching
Glass processing allows for relatively high-precision processing to be performed all at once, but it requires the use of strong chemicals and large quantities, making it relatively difficult to manage and control. There are also cases where the factory environment is poor. Wet blasting does not require these difficult-to-control chemicals, so it is relatively easy to control (abrasive concentration control, etc.) for stable production.
Comparison with Plasma
Since Plasma is an electrochemical reaction, the great advantage is that there is no residual foreign matter. However, it also has the disadvantage that it cannot be left alone for a long period of time due to time constraints after processing. Wet blasting, which is a physical process, does not have time dependence when imparting properties to the surface.
Glass Processing Examples Using Wet Blasting
Surface shape and surface roughness data from examples of glass processing by wet blasting using abrasives of various sizes.
Equipment Examples
We propose the following equipment according to the workpiece size and processing details. However, our equipment is essentially based on free design, in which the application and conditions are optimized for your company's processes. Our basic policy is to provide all our customers with optimal specifications. First, consult with us about the material and size of the workpiece, processing purpose, and equipment conditions. Our specialized staff will handle this.
Equipment for large-sized plate-shaped
- Automatic
Wet blasting equipment for thin plate-shaped materials that uniformly processes large-sized plate workpieces.
Equipment for plate-shaped workpieces
- Automatic
Automatic equipment for plate-shaped workpieces and film mateiral and is capable of processing plate workpieces up to 600 mm wide.