Removal of black scale and lubrication for cold forging
Processing Details
- Removal
- Roughening
- Scraping
Our proprietary technology for cold forging,
"WLS" has excellent lubrication performance and extends die life by five times.
Our proprietary “WLS” technology, which uses wet blasting, significantly improves die life in cold forging with lubrication performance that exceeds that of bonderizing. Furthermore, by replacing the bonderizing process, energy and management costs are reduced, and the environmental impact is reduced as well.
What is WLS?
WLS stands for "Wet blasting and dry-in-place type lubricant coating (Wetblast Lubricant System)." Our proprietary technology integrates degreasing, removing oxide scale and lubrication treatment for the cold forging process.
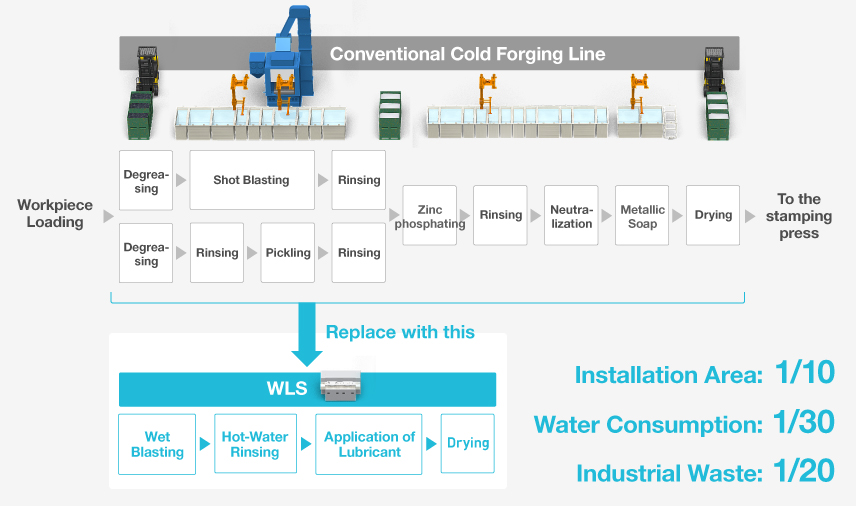
The WLS combines two processes in one machine: surface preparation using wet blasting and a lubrication process by applying a lubricant. In addition, compared with conventional bonderizing equipment, this process achieves surprising cost reductions of less than 1/10th the installation area, 1/30th the amount of water used, and 1/20th the amount of industrial waste.
What is Wet Blasting?
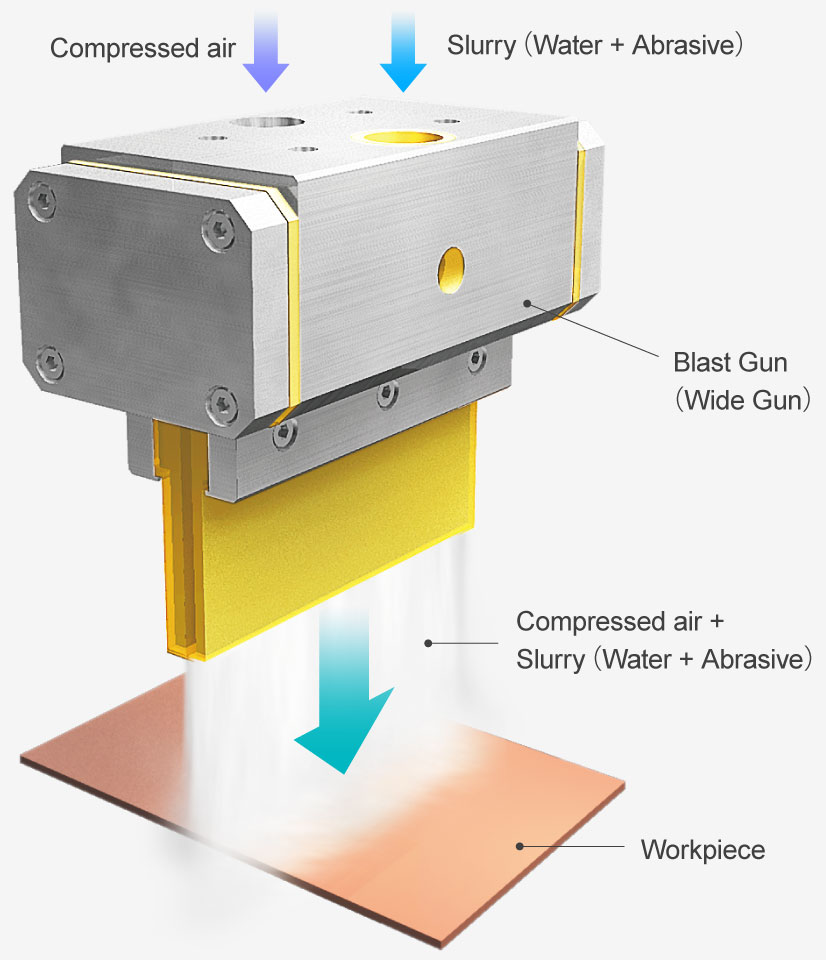
The "Wet Blasting" method used in "WLS" is a wet-type blasting process.
In "WLS", wet blasting is used to degrease the part, remove the black oxide scale, and do surface preparation prior to the lubrication process. Surface preparation by wet blasting maximizes the performance of the lubricants, achieving lubrication performance that exceeds that of bonderizing. Wet blasting is a physical surface-processing method. Another major benefit of adopting this method is that it can replace chemical treatment processes, which have a significant impact on the working environment.
Advantages of using WLS
The main advantages of replacing conventional processes with WLS are as follows.
Improvement of die life
The actual life improvement of dies is more than five times longer than that of conventional methods. This is because the surface preparation by wet blasting maximizes the lubricating performance of the lubricant coating.
Cost Reductions
The heavy and lengthy lubrication processes can be greatly simplified. Because lubrication is done by a spray application, daily maintenance only requires replenishing the abrasives and the lubricant.
Reduction of Environmental Impact
It completely replaces the bonderizing process, which has a large environmental impact. Compared to the bonderizing process, it can reduce reactive sludge to zero and waste by more than 90%.
By shifting from bonderizing to WLS,
CO2 emissions are reduced.
The introduction of WLS reduces the surface treatment by shot blasting and the transportation of containers by forklifts needed in conventional processes such as shot blasting and bonderizing. As a result of this process, annual CO2 emissions were reduced by 9.3 tons and daily power consumption was reduced by 87 kWh.
By switching to WLS, CO2 was reduced by
9.3 tons.
Daily Power Consumption (kWh/day)
Bonderizing Process | WLS | |
Lubrication | 505 | 538.4 |
Surface Treatment (Shot Blasting) *1 |
100 | - |
Forklifts *2 | 20.4 | - |
Total | 625.4 | 538.4 |
*1 Shot Blasting Prerequisites
※Lubrication conditions are based on Daido Chemical's calculations.
- 12,000 pcs/day=6,000 kg/day
- Shot Blasting Power Consumption: 10 kW (apron shot: 5.5 kW impeller + exhaust + apron drive)
- 200 kg per batch: 20 min per batch + 5 min for replacement
- 30 times per day
- 30 times x 25 min ÷ 60 min = 12.5 hours ⇒ Shot Blasting (2 units):15 times x 20 min operation per day
- Formula = 10 (kW) × 2 (units) × 15 (times) × 20 (minutes)/60 (minutes)
*2 Prerequisites for Forklifts
- Forklift capacitance is 20 kW (10 kW each for driving and cargo handling).
- Container capacity: Shot Blasting 400 pieces, Bonderizing 800 pieces, averaging 600 pieces
- Transportation time per one operation is 3 minutes.
Customer Feedback
Customers' opinions after WLS lines were introduced.
"Improved the life of the dies and had significant cost reductions."
Originally the WLS was introduced with purpose of replacing the bonderizing process and reducing WIP inventory. We knew that WLS creates an optimal base surface for lubricationl. But the mold life has also been greatly extended and the mold cost greatly reduced.
- Good lubricant film conformability due to fine surface roughness.
- Forging pressure is lowered by feeding the workpiece into the press at a temperature of 50 to 60°C.
"With WLS, we were able to realize the single-liquid process that we had given up on."
In order to produce parts in-house, we were looking for a process to replace bonderizing. We tried various white liquids on the surface after shot blasting to remove oxide scale, but they caused scratches. When I had given up saying that only black lubricants could be used, I learned about WLS. After doing a trial we realized that it could be done in one pass. I was surprised by the differences with the surface treatments.
- Removal of oxide scale after annealing is done simultaneously, which shortens the process.
"Reduces die defects caused by debris buildup in the dies."
When we were having trouble finding a company that could provide bonderizing treatment for a wide variety of materials, we were introduced to WLS. In addition to the ability of wet blasting to provide lubrication undercoating for a variety of materials, another deciding factor was the easy-to-manage spray-application method. Thanks to the thin, uniform coating, the frequency of die cleaning can be significantly reduced, and molded products are finished cleanly.
- A thin and uniform lubricating film is applied by spraying.
- Wet blasting can process any material.
Equipment Examples
We propose the following equipment according to the workpiece size and processing details. However, our equipment is essentially based on free design, in which the application and conditions are optimized for your company's processes. Our basic policy is to provide all our customers with optimal specifications. First, consult with us about the material and size of the workpiece, processing purpose, and equipment conditions. Our specialized staff will handle this.
Equipment for cold forging lines and billets
- Automatic
WLS equipment that cleans, descales, and lubricates billet materials.