Cleaning and pre-adhesion processing of anti-vibration parts
Processing Details
- Washing
- Roughening
Problems with traditional methods
(removal of grease → shot-blasting → warpage)
- Too much usage of chemicals and waste water.
- Dust is generated.
- Segmented processes cause failures in each process which leads to a lower production yield (low productivity). The size and length of each process leads to a lower utilization of space in the plant.
Solution (WBP)
(WBP:Wet Blast Phosphating system)
- We can generate uniform and precisie Phosphate layers which can prevent peeling, even at the bottle-neck processes.
- By using our exclusive method of transferring the metal parts, we can control and reduce waste water and chemical usage, thus reducing production costs.
- Because the wet blasting and phosphating processes are connected and continuous, concerns about contamination and oxidation between processes are eliminated. Thus you are able to maintain a stable and higher level of quality.
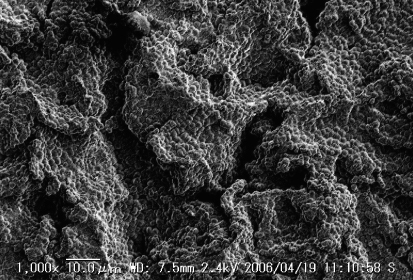
Wet Blast Phosphating system/SEM Surface
Wet Blast + Phosphate process
01
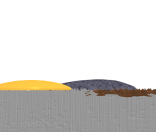
Untreated surface
There are oil, rust, and foreign particles on the surface.
02
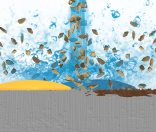
Wet Blast process
By using compressed air to spray a mixture of water and abrasives onto the part’s surface, degreasing, removal of rust and foreign particles, and surface roughening are all done simultaneously.
03

Water Rinse
The surface is now activated after cleaning and is covered by a film of water.
04
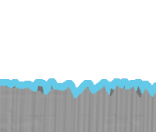
Phosphate
A rust-proof and precise phosphate layer with superior adhesion is created.
Process
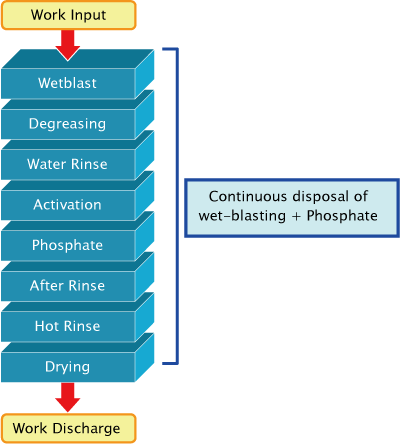
Utilization Results
Disc Brake (Before)
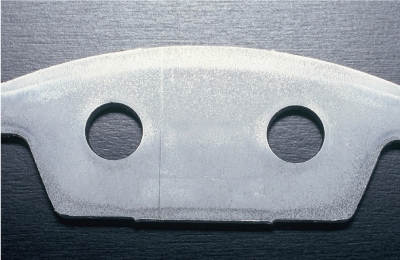
Disc Brake (After)
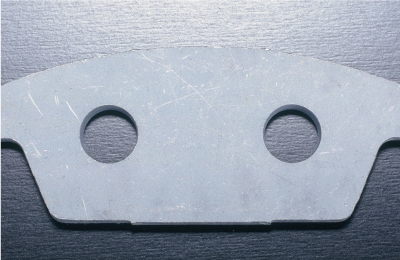
Metal Parts (Before)
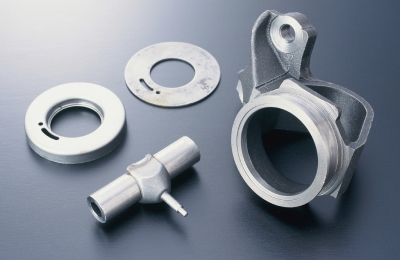
Metal Parts (After)
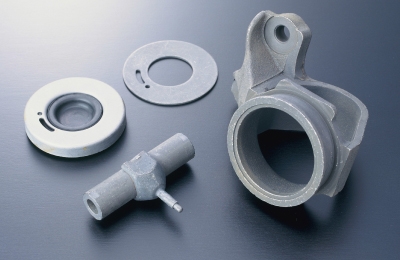