Precision deburring of resins and metals
Processing Details
- Roughening
- Washing
- Scraping
Damage-free removal of fine burrs with soft, ultra-fine abrasives.
This is an example of removing resin burrs from a heat sink using wet blasting. Wet blasting, which can use fine abrasives of a few microns or smaller, is suitable for removing fine burrs, and is characterized by achieving a finish without damaging the target part.
Contents
What is a burr?
Burrs are protrusions such as jagged edges or spikes that are unintentionally created during the processing of resins and metals.。
A wide variety of burrs are generated in various situations, such as "plastic molding burrs" or "casting burrs" where the material seeps out of the mold gaps during molding, and "cutting burrs", "grinding burrs" or "shear burrs", which occur during the processing of metal (cutting, grinding, shearing, drilling, polishing, etc.).
Also, JIS B 0051 defines it as "residue on the outer corner edges of a geometric shape and on parts during machining or forming processes."
What is deburring?
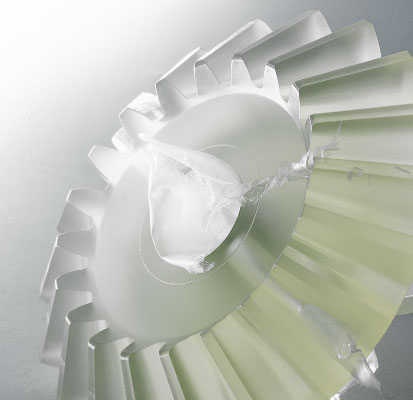
Deburring is the removal of various types of burrs.
Burrs are unintended shapes that can cause various problems.
Many problems are possible, such as dimensional accuracy problems during product assembly, quality and performance variations and degradation, adverse effects on subsequent processes when debris is mixed in as fine dust, damage to objects that come into contact with the material, and damage due to entrapment in the equipment used for processing. Therefore, it is necessary to remove these burrs in various manufacturing processes.
However, there are many types of burrs, including their size (expressed in height and thickness at the base), material and shape, and the location where they occur, making it difficult to define an effective deburring method for all cases.
Common Types of Deburring
Common deburring methods include the following
Manual work with blades and tools
Using special cutters and tools, the worker in charge manually removes the burrs. The advantage is that it can be done without any equipment, but the disadvantages are that it takes a lot of man-hours and the quality of removal tends to depend on the individual.
Brushing, Buffing, Belt Polishing
Burrs are removed by bringing the workpiece into contact with brushes, buffers, or belts that rotate at high speed or move back and forth. In many cases, this is a burr removal method that can be performed without requiring relatively large equipment. However, depending on how contact is made, directional scratches may remain on the workpiece.
Barrel Polishing
Barrels and abrasive particles (abrasives, projection material, media, compounds) are used. The workpieces and abrasive materials are placed in a barrel, and the barrel is rotated to bring the workpieces into contact with the abrasive materials to remove the burrs. Although it is suitable for mass-produced products because it can process a large number of objects at one time, there are disadvantages such as scratches and deformation of parts.
Blasting
This is the removal of burrs by sand (air) blasting, shot blasting, or wet blasting. Similar to barrel polishing, abrasive materials are used, but the parts are processed by blasting with air or an impeller. Depending on the method, fine adjustments and uniformity are possible. However, special equipment is needed, and relatively high initial and running costs are required.
Water Jet
This is a process that projects water under high pressure and is suitable for deep holes that are difficult to reach with other machining processes. Since only water is used, there is little damage to the surface of the object and a wide variety of objects can be processed. However, there is a possibility of deformation of the object, water-soluable materials cannot be handled, and its accuracy may be inferior to that of machining.
Thermal Deburring
This method uses combustible gases. After being pressurized in an airtight container, the burrs are incinerated by instantaneous gas combustion. It is effective even inside complex hole shapes that cannot be reached with other tools or methods. However, in addition to relatively large facilities and equipment, strict safety controls are required.
Electrolytic Processing
Chemical burr removal using electrolysis. Also called electrolytic deburring or electrolytic polishing. Even complex shapes that are difficult to machine can be processed by using an electrode jig. Disadvantages include that the machining accuracy may be unstable for various reasons, and that the part cannot be processed unless it is conductive.
Chemical Processing
Scientific deburring using chemicals. The entire surface of the workpiece, including burrs, is dissolved. It is effective even for complex shapes, and it is possible to carve uniformly into areas that come into contact with chemicals, but strict control is required as toxic gases are generated and chemicals that are dangerous to the human body and the environment are often used.
Lasers
The burrs are burned off by laser irradiation. It can handle materials such as resin products, non-metals, glass, and ceramics, and can deburr without touching the workpiece. However, if the burrs are thick, it may be difficult to focus, and there is a risk of burning and damaging the part. Furthermore, burnt burrs turn into soot and adhere to the frame, so cleaning is required afterward.
Fine deburring of resin and metal by wet blasting
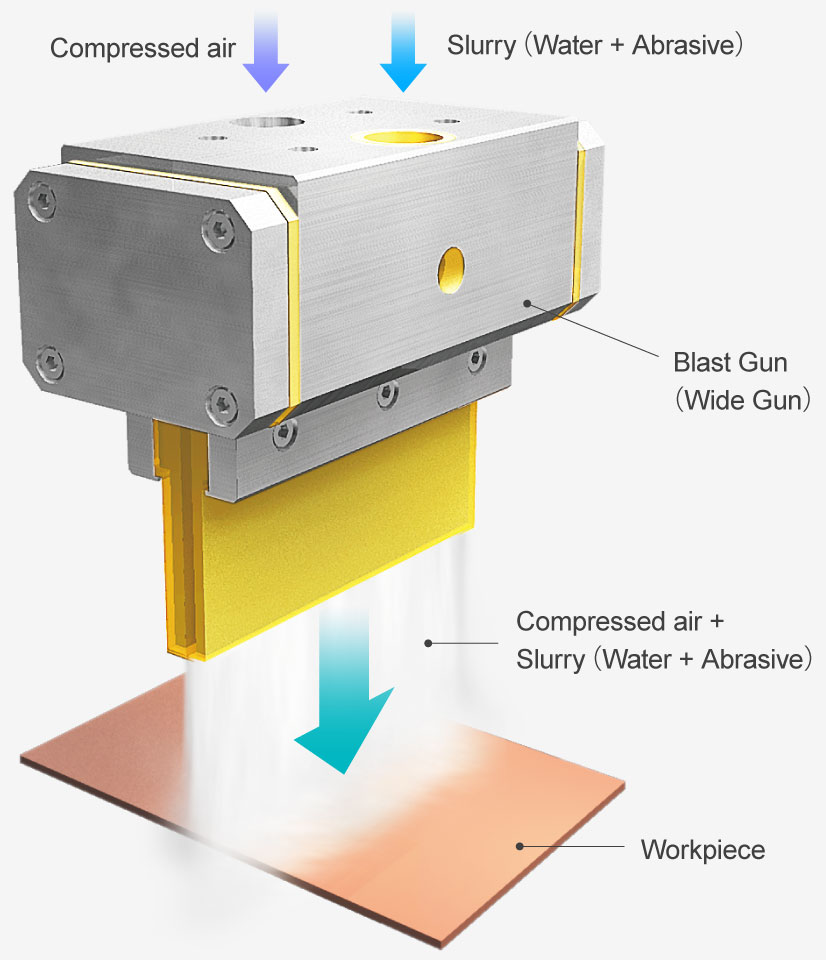
Deburring by wet blasting is classified as blasting, in which a slurry mixture of abrasive and water is projected by air to remove the target burrs.
Wet blasting, which can use fine abrasives smaller than several microns in size, is suitable for removing fine burrs. Conversely, it is not suitable for removing large burrs due to their strong adhesive strength.
Features of Deburring by Wet Blasting
Wet blasting for removing fine burrs from resin and metal has the following features.
Damage-Free Processing
Wet blasting can use fine abrasives of several microns in size, making it possible to process objects with less unnecessary damage. No directional scratches are generated due to processing with loose abrasives.
Easy automation and labor savings
Wet blasting, which does not require degreasing, can be used for cleaning, and can handle workpieces of various shapes, making it easy to automate equipment and save labor. It is easy to adapt to a line production system by installing a loader and unloader, and the daily management of the equipment is simple, basically just managing the slurry concentration.
Precision Processing
Thanks to its feature of being able to use fine abrasives, wet blasting is suitable for removing fine burrs 0.1 mm or smaller. It is particularly effective for treating minute objects such as electronic components, tools, and the cutting edges of medical instruments, and is suited for delicate burr removal while minimizing damage to the workpiece surface.
High Controllability
Unlike sand (air) blasting, which handles abrasives in powder form, wet blasting uses water as a medium to project abrasives in a fluid. This makes it easy to precisely control the processing force. Because of its high reproducibility, it is effective in suppressing variations in quality and improving yield.
Compatible with complex shapes
Wet blasting, which allows the use of fine abrasives several microns in size and handles the abrasives in a fluid, is effective even on complex-shaped objects with narrow gaps. However, depending on the inside of the pipe or the size of the hole, the projection may not reach the target area and effective treatment may not be possible.
Processing Examples
Removal of sideburrs from diodes
- By using a resin abrasive, even firmly attached burrs can be quickly removed.
- Damage-free removal is possible without causing scratches or deformation on the lead frame or package surface.
Removal of resin burrs from transistors and heat sinks
- By using a fine abrasive material, resin burrs on heat sinks can be quickly removed.
- Damage-free removal is possible without scratching or deforming delicate objects.
Removal of cutting burrs from the edges of unevenly shaped parts
- A soft resin abrasive can be used to remove cutting burrs from the edges without damaging the surface.
R honing of carbide cutting tool edges
- Adds a fine radius (R) to the edge of cutting tools that are prone to chipping, thus preventing chipping and extending the tool life.
Removal of hob cutter edge burrs caused from machining
- Usage of fine abrasives enables quick removal of even fine burrs
- Damage-free removal is possible without scratching or deforming even delicate objects.
Removal of hob cutter return burrs after the machining process
- It is possible to remove the after-machining return burrs without deforming the edges.
Erasing parting lines from resin molds
- Parting lines that occur after molding can be removed without damaging the resin.
Comparison with Other Methods
Differences between wet blasting and the following common methods.
Comparison with manual work that uses blades and tools
Labor savings is easily achieved because wet blasting is done with automated equipment, thus enabling deburring of the same quality in a shorter time and with fewer workers. In addition, stable processing quality can be maintained with high reproducibility.
Comparison with brushing, buffing, and belt polishing
Proper slurry management ensures uniform quality with stable processing power.
Comparison with Dry Blasting
Wet blasting is good at fine surface processing. It also generates no dust, heat, or static electricity.
Comparison with Electrolytic and Chemical Processing
Wet blasting is a physical process that does not use chemicals. A wide variety of materials can be processed in a good working environment.
Demerits of Wet Blasting
Deburring by wet blasting has the following weaknesses and disadvantages.
Processing is only done to the areas where the slurry hits.
Wet blasting can only process areas directly impacted by the abrasive in the slurry. Therefore, it is difficult to process narrow and long gaps and the inner surface of tubes.
Not suitable for hard and large burrs
Although fine abrasive material allows precise machining, the machining force is relatively weak, making it unsuitable for removing large burrs with strong adhesion.
Equipment Examples
We propose the following equipment according to the workpiece size and processing details. However, our equipment is essentially based on free design, in which the application and conditions are optimized for your company's processes. Our basic policy is to provide all our customers with optimal specifications. First, consult with us about the material and size of the workpiece, processing purpose, and equipment conditions. Our specialized staff will handle this.
Equipment for plate-shaped workpieces
- Automatic
Compact automatic equipment for simultaneous double-sided processing of lead frames and other thin plate-shaped workpieces.
Equipment for testing
- Semi-automatic
Equipment with an articulated robot and servo-controlled rotary table that can handle a wide range of tests.
Index-type equipment
- Semi-automatic
A wide-gun, 2-stage, index-type equipment that can process and set at the same time.
Equipment for cutting tools
- Automatic
Automatic machining equipment that performs high-precision cleaning and surface treatment of cutting tools, and R-honing and such of cutting edges.
Equipment for cutting tools
- Automatic
Wet blasting equipment for cutting tools that can automatically control the cutting edge shape (K-value).
Manual wet blasting equipment
- Manual
Compact wet blasting equipment that is ideal for cleaning.
Manual wet blasting equipment
- Manual
Highly wear-resistant and versatile manual equipment that is a step up from MRB-7.
Manual wet blasting equipment
- Manual
Large manual equipment that can handle large and heavy objects and reduces costs through lot production.