Removal of Drill Droplets
Processing details
- Washing
- Removal
It is possible to remove droplets that cause galling and seizure without creating holes in the coating film.
Wet blasting has also been used extensively to remove droplets from cutting tools without causing any damage after the tool has been coated. At the same time, this processing can also reduce surface roughness.
Drill Droplet Removal with Wet Blasting
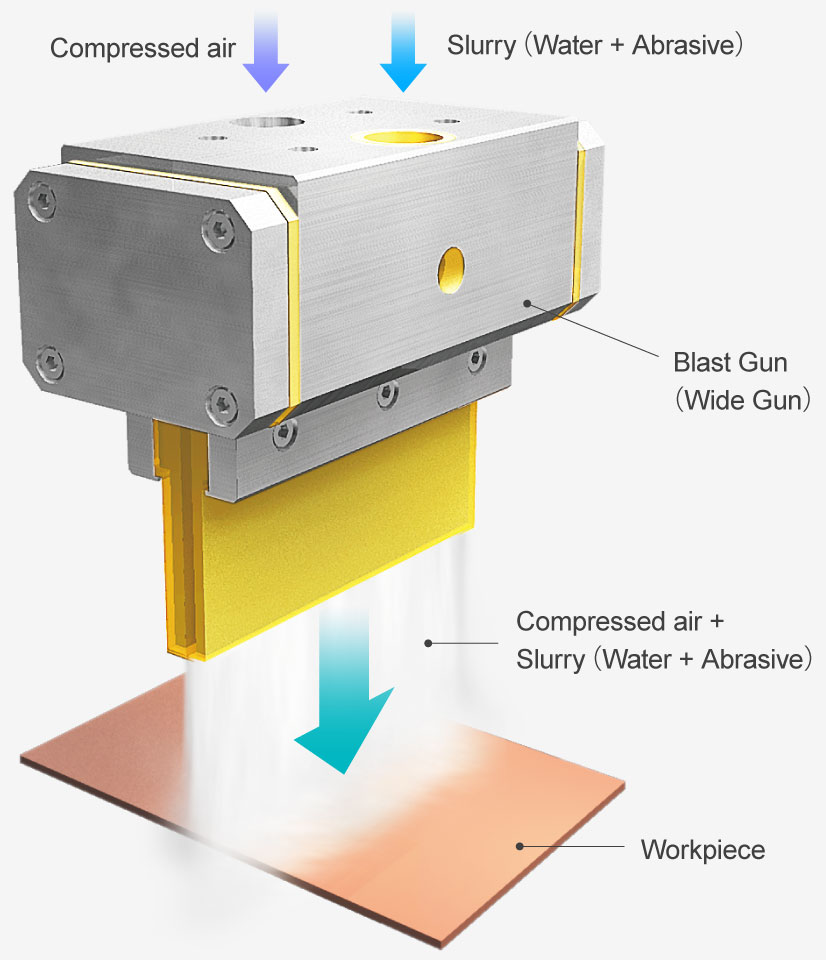
Droplets (granular protrusions and particles) generated on the coating, such as PVD applied to the cutting tool surface, are removed without damaging the coating film, improving welding resistance and defect resistance.
It also relieves the tensile stress on the CVD-coated surface, improving the wear resistance of the cemented carbide tip's cutting edge.。
Processing Points
- Droplets can be removed without making holes in the coating film.
- Effective for complex-shaped parts that hands or polishing instruments cannot reach.
- Surface roughness can be reduced by smoothing the surface at the same time as removing droplets.
Problems with conventional processing methods
- There are some areas of 3D workpieces that are difficult to polish using a polisher.
- When droplets are removed, the coating film is also scraped off.
- Difficult to automate polishing process.
- Galling and seizure occur when using cutting tools.
Before and After Processing Comparison
The removed droplets are invisible to the naked eye, but the treated surface has no scratches and is shiny.
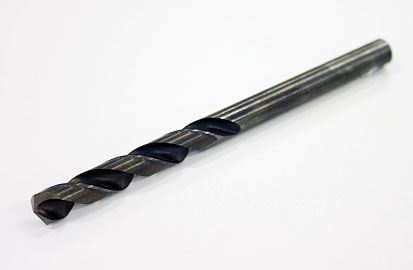
Before Processing
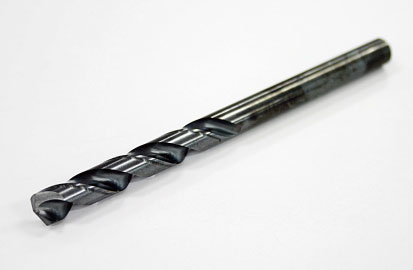
After Wet Blasting
Enlarged Surface Image
Laser Microscope
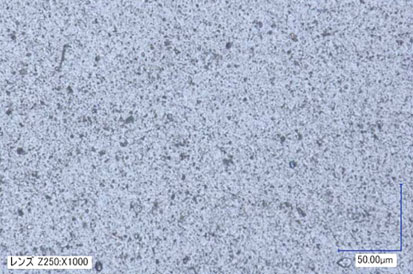
Before Processing Ra: 0.24 µm Rz: 1.60 µm
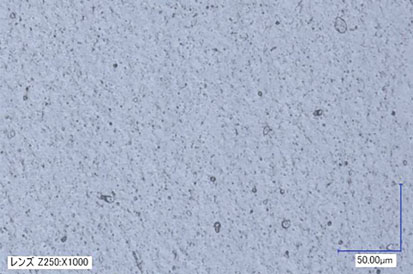
After Wet Blasting Ra: 0.16 µm Rz: 0.95 µm
SEM
The black dots are the droplets. *Dots that appear black after processing are remnants of degranulation (depressions where droplets were removed).
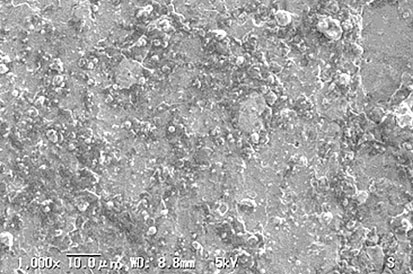
Before Processing
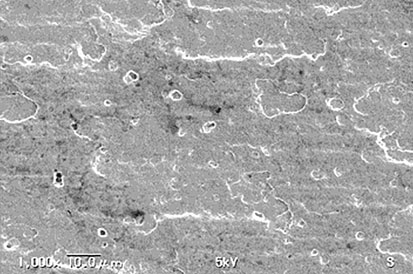
After Wet Blasting
Surface Roughness
Wet blasting conditions: MP-200 (abrasive), 0.4 MPa (air pressure) , 30 sec (processing time)
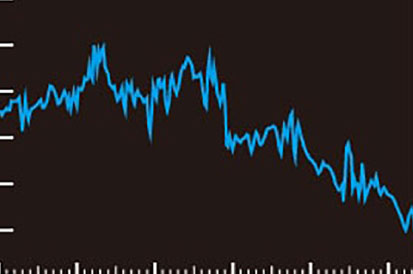
Before Processing Ra: 0.413 µm Rzjis: 0.974 µm
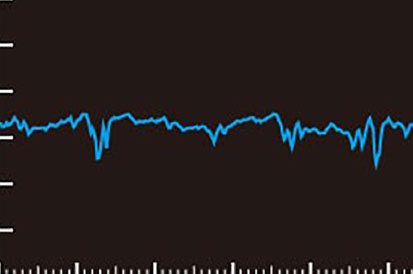
After Wet Blasting Ra: 0.063 µm Rzjis: 0.336 µm
Equipment Examples
We propose the following equipment according to the workpiece size and processing details. However, our equipment is essentially based on free design, in which the application and conditions are optimized for your company's processes. Our basic policy is to provide all our customers with optimal specifications. First, consult with us about the material and size of the workpiece, processing purpose, and equipment conditions. Our specialized staff will handle this.
Equipment for cutting tools
- Automatic
Automatic machining equipment that performs high-precision cleaning and surface treatment of cutting tools, and R-honing and such of cutting edges.
Equipment for cutting tools
- Automatic
Wet blasting equipment for cutting tools that can automatically control the cutting edge shape (K-value).
Line-production equipment for cutting tools
- Automatic
Multi-gun type batch-processing equipment that performs surface treatment of cutting tools loaded in pallets.
Line-production equipment for cutting tools
- Automatic
Equipment with a wide gun that does batch processing and performs surface treatment of cutting tools loaded in pallets.