Differences with Sandblasting
Wet blasting and sand blasting (dry blasting, shot blasting) are very similar methods in that they "process the surface of the object by projecting countless abrasive particles".
However, they differ greatly in terms of the size of the abrasive that can be handled, residue, processing accuracy, and other aspects.
Differences between wet blasting and sandblasting
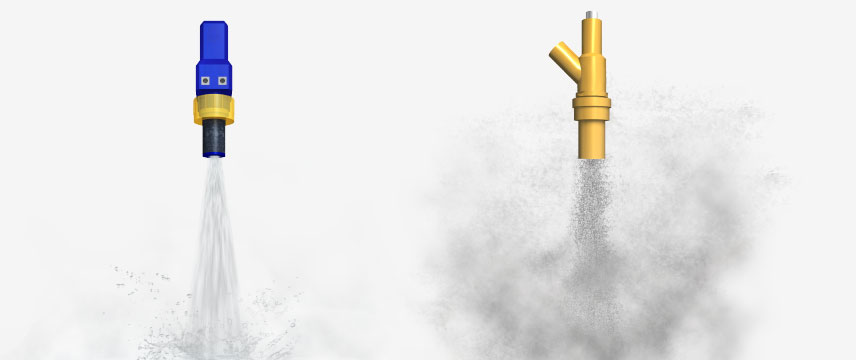
Since wet blasting uses water, has a high degree of cleaning power, and can handle fine abrasives, it can perform uniform processing with high precision.
However, the processing power is relatively weak, and it takes time to remove thick paint and such.
In addition, the equipment price is relatively high because the mechanism is more complicated than that of sandblasting.
Sandblasting, on the other hand, uses compressed air to blast only abrasives without water.
It is characterized by high processing power because it handles comparatively large abrasives.
However, it differs from wet blasting in that it generates "dust" that is scattered by the blasted abrasive, and it is not good at uniform processing.
In addition, since there is no degreasing effect, separate degreasing and drying processes are required as pretreatments.
Comparison between wet blasting and sandblasting
Abrasive Size
Generally, the lower limit of the abrasive size that can be handled by sandblasting is about 50 microns.
Wet blasting, on the other hand, can handle extremely small abrasives of a few microns in size.
Abrasive Residue
In sandblasting, a phenomenon occurs in which the abrasive material strikes other abrasive material causing residue to be embedded in the surface.
In wet blasting, after processing the abrasive material is washed away by the water, so there is very little residue.
Processing Accuracy
With sandblasting it is easy to adjust pressure and it achieves high-precision processing. However, it is less controllable than wet blasting.
Wet blasting excels at high-precision, accurate and uniform processing because it is fluid-controlled and can use very fine abrasives.
Degreasing Effect
Sandblasting has no degreasing effect.
Therefore a pretreatment degreasing process is needed.
Wet blasting scrapes off a thin layer from the surface together with oil, so it is possible to do degreasing and processing at the same time.
Furthermore, since a film of water instantly covers the scraped surface, there is no re-adhesion of the oil.
Processing Heat
In sandblasting, processing heat is generated by the friction between the abrasive material and the workpiece.
In wet blasting, the workpiece retains no heat because water constantly cools the surface during processing.
Static Electricity
In sandblasting, static electricity is generated by friction.
Therefore, separate measures against static electricity are necessary.
In wet blasting, the workpiece is not charged with static electricity because the electricity escapes into the water.
Secondary Pollution
Sandblasting can cause secondary contamination of the workpiece to be processed due to the collision of dirty abrasives with the workpiece.
With wet blasting, this does not occur because a water film covers the new surface after processing and prevents the reattachment of dirty material.
Secondary Processing
Although it cannot be done with sand blasting, with wet blasting secondary treatment can be done by just mixing in chemicals such as rust inhibitors or degreasing agents into the slurry.
Work Safety
With sandblasting, dust is generated by the scattering of abrasives, thus equipment such as dust collectors are required.
Dust can also pose risks of fires or dust explosions. Wet blasting does not generate any dust.